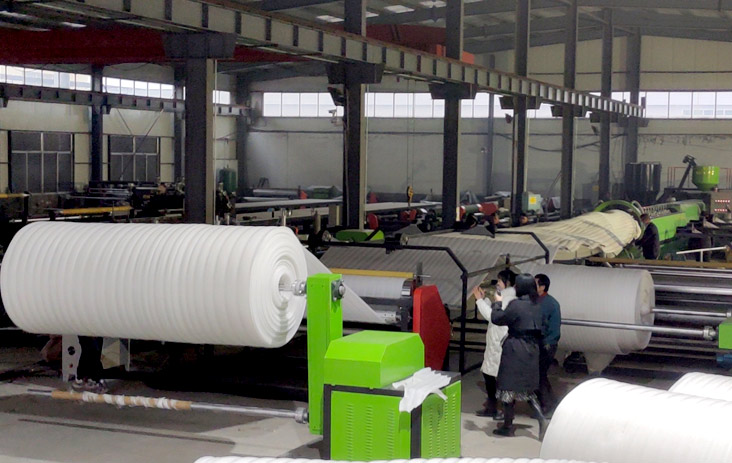
power source request:power voltage is 380V,50Hz(based on customer request),three-phase four wire system. The transformer capacity is confirmed according to the production line installed capacity.
1.1The plant area will be confirmed based on the production line length, and it must be with the good ventilation and exhaust function, the workshop lighting should adopt the explosion-proof lamp and switch.
1.2 Preparing enough the raw material and auxiliary material, it is polyethylene raw material, monostearin, talcum powder, and butane, nitrogen.
1.3 Preparing enough paper tube with inner diameter is 72-76mm.
1.4 Preparing enough blade, and a quantity of cotton gloves
1.5 Open flame is strictly prohibit in plant, do good fire warning signs, preparing the fire extinguisher and other fire prevention tools.
2.The inspecting work before installation
Inspecting every parts is all ready and not, damaged or not, lost or not.
3 Installation
3.1 Cleaning the floor in plant
3.2 Placing every parts according to the production line request, the order is: extruder, sizing parts, flatten part, traction device, rolling device.
3.3 Setting well the butane pump in pump room, and connecting with pipeline, the order is: nitrogen gas bottle, butane tank, air tank, butane pump, the extruder one-way valve.
3.4 Placing the monostearin part on the side of extruder, connecting it with the one-way valve of extruder with pipeline.
3.5 Placing the control cabinet one the side of the reducer of extruder, auxiliary control cabinet on side of the tractor sprocket, and connecting the controlling wire line of each part with the thermocouple.
3.6 Adjusting the anchor top silk of the main engine and the auxiliary engine.
3.7 Installing the feeding platform, and placing the feeding ladder together on side of the extruder reducer.
3.8 Installing the wind ring and fan, connecting with the sizing drum fan, connecting the butane pump and the monostearin pump with wire line.
3.9 Feeding water to water pump, adjusting the water pump.
3.10 Installing the plastic granule feeding machine and the talcum powder feeding machine, connecting with power.
311 Rewind shaft.
Notice: The extruder and every auxiliary machine must be connected with ground wire. (using diameter 6-8mm rebar to tandem the main and auxiliary machine , and connecting with ground . )
3.12 Adjusting main motor frequency conversion according to the direction, to prohibit the rollover, running frequency is source from the external terminals.
3.13 Inspecting main motor, butane pump, monostearin pump, wind ring fan, sizing drum fan, cutting motor, and traction motor, two rolling roller and the turning or the fan of two torque motor, to make it turn at forward direction.
3.14Adding lubricating oil for every reducer, pump, and chain. Adding hydraulic oil for hydraulic station.