What is EPS (expanded polystyrene)?
Expanded polystyrene (EPS), also called expandable polystyrene (EPS), has the advantages of low relative density (1.05 G/cm3), low thermal conductivity, low water absorption, shock and vibration resistance, heat insulation, sound insulation, moisture resistance, vibration reduction, excellent dielectric properties and so on.
It is widely used in shockproof packaging materials for mechanical equipment, instruments, household appliances, handicrafts and other vulnerable valuable products, as well as packaging of fast food. With the rapid development of global economy, the waste of polystyrene foam is increasing day by day. These waste polystyrene foams are characterized by light weight, large volume, aging resistance and corrosion resistance, which have become a major problem in waste disposal. In recent years, the recycling of polystyrene foams has become one of the most concerned issues in the industry.
Process for preparing expanded polystyrene
Molding process of expanded polystyrene
How is foamed polystyrene made step by step?
Foaming principle of expanded polystyrene
Expanded polystyrene first foaming (pre-foaming)
Secondary foaming of expanded polystyrene (molding process)
Main application of expanded polystyrene
Expanded Polystyrene Storage and Transportation
Regeneration of expanded polystyrene
Advantages of expanded polystyrene
Disadvantages of Expanded Polystyrene in Construction
Is expanded polystyrene dangerous?
Is expanded polystyrene harmful to human body?
Process for preparing expanded polystyrene
There are two main preparation processes of EPS particles:
1) One-step impregnation process (one-step method for short). In that one-step method, styrene monome, initiator, dispersing agent, wat, foaming agent (common foaming agents include pentane and butane) and other auxiliary agent are added into a reaction kettle, resin particles containing the foaming agent are obtained after polymerization, and expandable polystyrene bead products are prepared by washing, centrifugal separation and drying;
2) Two-step impregnation process (referred to as two-step method) is to polymerize styrene monomer into polystyrene beads with a certain particle size, classify and screen them, then add water, emulsifier, foaming agent and other additives into the reaction kettle, heat and impregnate them to obtain expandable polystyrene beads.
This method is also called post-impregnation method. The one-step process is characterized by simple process and low investment cost, and is superior to the two-step process in terms of reducing consumption and saving energy consumption. At present, the production process of expandable polystyrene abroad is mainly one-step method, which is suspension method.
Molding process of expanded polystyrene
There are also two main EPS molding processes: 1) one-step extrusion route, in which EPS particles are directly extruded after foaming, which is mostly used to make sheets and films; 2) a molding route, firstly pre-foaming the EPS particles by 30 to 50 times with air (or water vapor) at 100 deg C, then curing the EPS particles by standing for 24 hours, placing the cured pre-foamed material in a mold made of aluminum or a casting, heating the material by air (or water vapor) at 115 to 120 deg C, The surfaces of the particles are fused with each other by the action of heat to form the foam plastic part.
How is foamed polystyrene made step by step?
The first foaming of expanded polystyrene, called prefoaming, involves expanding individual EPS crystal particles into swollen monomer particles.
The steam also penetrates into the already expanded voids, increasing the overall pressure within the voids. As steam is introduced, the pressure and volume of the beads increase steadily. If steam is constantly applied to the beads, their volume will continue to expand until every thin wall of the void is broken.
Continued vapor penetration during prefoaming is critical because the rate of vapor entry into the void must exceed the rate of escape of the blowing agent from the void. This prevents the blowing agent from escaping, stretching the polymer into a rubbery state with sufficient strength to balance the internal pressure, thereby achieving pre-foaming.
The beads must remain dispersed and free flowing throughout the process, usually by continuously mixing the beads and steam in an agitated vessel.
importance of vapor permeation: During the pre-foaming process, continuous vapor permeation is critical, which increases the total pressure within the void. This ensures that the blowing agent remains within the void, stretching the polymer like a rubber, equalizing the internal pressure and achieving pre-foaming. This process requires that the beads remain dispersed and free flowing.
Age: storing that pre-expanded bead
After pre-foaming, the beads undergo a period of storage, known as an aging period, to absorb air. During aging, the beads are cooled by air, causing the blowing agent and water vapor in the voids to condense into a liquid, creating a vacuum in the voids.
Generally speaking, the lighter the foam density, the shorter the aging time, while the higher the foam density, the longer the aging time.
Foamed polystyrene secondary foaming: molding process
The second foaming, also known as the molding process, consists of two stages of steam heating and cooling shaping. After aging, the pre-expanded beads were subjected to steam heating.
At this point, the polymer softens and the pressure inside the void exceeds the external pressure, causing the bead to expand again. The expanded beads fill the gaps between them and form a solid block of the same shape as the mold. This produces a foam product which is then cooled with water for final curing.
Summary Understanding the step-by-step manufacturing process of expanded polystyrene provides insight into the complex process of making this versatile and versatile material. From pre-foaming to molding, each stage affects the characteristics and application of the final product.
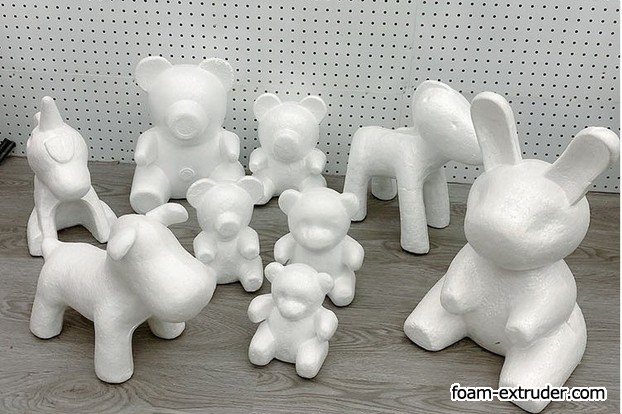
Main application of expanded polystyrene
Expanded polystyrene (EPS) has the advantages of low relative density (1. 05 G/cm3), low thermal conductivity, low water absorption, shock and vibration resistance, heat insulation, sound insulation, moisture resistance, vibration reduction, excellent dielectric properties and so on. It is widely used as shockproof packaging materials for mechanical equipment, instruments, household appliances, handicrafts and other vulnerable valuable products, as well as the packaging of fast food.
Expanded Polystyrene Storage and Transportation
EPS products are usually safe and non-toxic, but the raw materials in different States during processing are dangerous. Polystyrene powder can irritate the respiratory tract and skin. EPS particles in storage emit pentane vapors, which are highly flammable and form explosive mixtures with air. Heating a polystyrenic polymer may release styrene monomer, which is a dangerous substance.
Regeneration of expanded polystyrene
1) recycling and pelletizing: reducing the volume of the EPS waste by using processes such as heating densification, cold crushing or cold compression and the like, and then re-pelletizing. Then the prepared EPS particles are directly used or the EPS particles are mixed with other high polymer raw materials (such as linear SBS) to be processed into plastic alloy to manufacture plastic products, such as clothes hangers, flowerpots, video tapes, furniture, building materials or thermal insulation materials.
(1) a light roof thermal insulation material;
(2) a concrete foaming thermal insulation board;
(3) a fiber reinforced sound insulation thermal insulation board;
(4) a plant fiber reinforced thermal insulation material;
(5) a sound insulation thermal insulation brick.
6) dissolving the EPS waste in a solvent to be directly used as a coating, an adhesive or a caulking agent:
(1) specially treating the waste polystyrene foam plastic to produce a novel water emulsion coating taking water as a medium, and using the water emulsion coating as an ideal moisture-proof finishing agent for corrugated boxes; And
(2) dissolve that styrene foamed plastic in aromatic hydrocarbon, chlorinate hydrocarbon, aliphatic ketone or ketone, adding an auxiliary agent after a certain concentration is reached, uniformly stir to produce the waterproof coating, and adding different pigments to obtain the colored coating, wherein the colored coating can be sprayed on the outer wall or the cement floor of a building, and the outer layer of a packaging box or a packaging box to play a waterproof role.
Advantages of expanded polystyrene
Energy Efficiency: EPS insulation significantly improves the energy efficiency of buildings by providing excellent insulation. This means lower heating and cooling costs throughout the life of the building. In addition, it is light and easy to carry and install, thus further improving the construction efficiency.
C: Durability and longevity: EPS insulation is known for its durability and adaptability to moisture, chemicals and physical shocks. Its ability to maintain performance over time ensures the life of the building structure, reducing the need for frequent maintenance or replacement.
D: Cost-effectiveness: EPS insulation is a significant benefit, making it an attractive option for residential and commercial construction projects. Its affordable price, combined with its energy-saving features and long-term durability, makes it an excellent investment.
The advantages of Expanded Polystyrene (EPS) are diverse and indispensable in various industries, especially in the fields of construction and insulation. EPS has excellent insulation properties that significantly improve energy efficiency and reduce heating and cooling costs. It is light in weight, easy to carry and install, and simplifies the construction process. Its versatile EPS allows customisation in a variety of shapes and sizes, with tailor-made solutions to meet specific project needs.
Disadvantages of Expanded Polystyrene in Construction
Although the application of expanded polystyrene (EPS) thermal insulation materials in buildings has some obvious disadvantages. Challenges include susceptibility to compression, limited fire resistance, and environmental concerns due to its petroleum-based origin and non-biodegradable nature.
In addition, EPS may attract pests and have limited load-bearing capacity, requiring careful consideration and mitigation strategies during construction projects. Understanding these drawbacks is critical for architects, builders, and homeowners seeking effective insulation solutions that balance performance with environmental and safety concerns.
Is expanded polystyrene harmful to human body?
Expanded polystyrene is usually harmless to human body under normal use, but it may have adverse effects on human health under certain conditions.
Expanded Polystyrene (EPS) is a kind of macromolecule material which is widely used in packaging and building materials.
EPS is non-toxic, but it decomposes at high temperatures and releases harmful gases, such as styrene, benzene and carbon dioxide, which may be harmful to human health. In addition, expanded polystyrene may leave chemical residues in the production process, such as benzene, etc. Long-term exposure to these substances may lead to skin allergies, respiratory irritation and other problems.
Avoid high temperature heating: Do not place expanded polystyrene products in high temperature environment, especially avoid heating food.
Reduce direct contact with food: try to avoid using expanded polystyrene products to hold high-temperature food or beverages.
Choose environmentally friendly materials: When buying foamed polystyrene products, choose products with reliable quality and environmental protection.
Standardized operation: strictly follow the operating procedures during construction, and maintain good ventilation conditions to reduce the release and inhalation of harmful substances