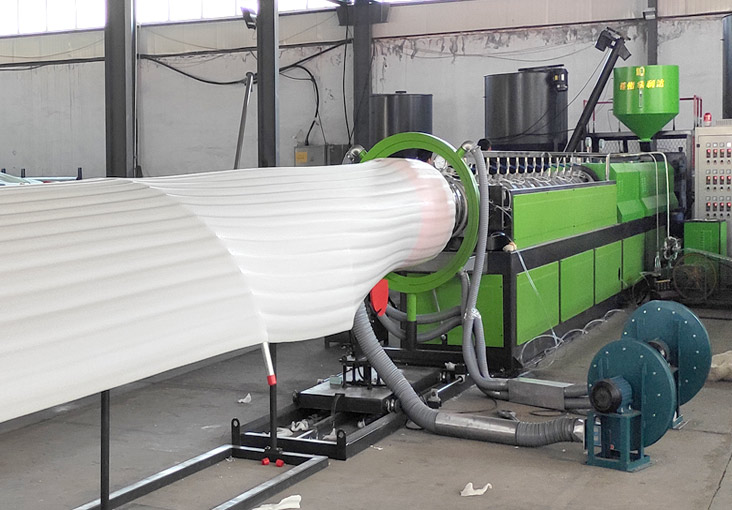
a.Turn on the main cabinet power switch, turn on the branching power switch, checking if the temperature controller is normal in each zone, once finding the abnormal occurrence, to solve it immediate. Adjusting the temperature controller data to the requirement temperature, the initial setting temperature can refer the following file:
zone |
Monostearin pot |
Monostearin pump and pipeline |
The 1st zone of barrel(beginning from the hopper) |
2nd zone of barrel |
3d zone of barrel |
4th zone of barrel |
5thzone of barrel |
6th zone of barrel |
7th zone of barrel |
8th zone of barrel |
Screen changer |
Machine head |
Temperature C° |
90-100 |
90 |
100 |
180 |
180 |
170 |
170 |
170 |
170 |
170 |
180 |
180 |
b.Turning on the heating switch of every zone, checking if the ammeter value of every zone is regular, if the current value is less than rated value, it stands that this heater maybe damaged of this zone, and it should be change immediate.
c. When the temperature of each zone is reached the set data, insulation for about half an hour, to let the temperature outside of the screw barrel and inside one uniform, to ensure the raw material of barrel be fully melted.
d.Checking if the monostearin is enough.
Ready to start EPE foaming machine(Expanded polyethylene machine)
a.After Preheating, open each valve of the nitrogen bottle , butane gas bottle, reduced pressure tank, and one-way valve one by one, adjusting the pressure value of nitrogen gage to 1.3-1.4Mpa, checking if there is leaking, one there is leaking, taking action to solve it immediate. Checking the flowing of butane pump, if the butane pump is frequency control, then checking if the PM knob is in the low frequency location, if it is not frequency control, then checking if the flowing control valve is in the low flowing location.(generally it is 16%)
b.Checking if the monostearin flowing control valve is in the low flowing location, generally the ticking is at the 6 location.
c.Turning on the water pump switch, checking if the water pump is in normal working.
d.Covering the paper tube on rolling machine two rollers, and tightening up.
Starting EPE foaming machine(Expanded polyethylene machine)
a.Setting the cooling temperature.
Modify the 1st, 6th , 7th , 8th screen changer, and adjusting the machine head temperature to cooling temperature. Generally, the first zone is 130 C°,the 6th , 7th, 8th zone is set by the actual data when testing running.
b.Main engine staring
Click the main engine starting button, when the frequency conversion is showing stable, adjusting the FM knob to 8HZ, at this time, the engine machine has been started.
Notice: don’t starting the machine when the temperature is not enough, otherwise, there will be the dangerous of twist off the screw.
c.Starting the butane and monostearin pump.
Click the butane and monostearin pump starting button, seeing if the butane and monostearin pressure is normal, if there is abnormal condition, taking action to solve immediate, the details action please refer the failure analysis table.

Starting the EPE foaming machine(Expanded polyethylene machine) cooling system.
a.1Barrel cooling part
Open the water valve of 6th , 7th , 8th zone, adjusting the flowing value of each water valve, cooling for this three zones, notice the water flowing should be proper, if the flowing more less, then the cooling will be slower , then need much time to cooling, so that it can waste more material; if the fowling is more, then the cooling speed is much faster, because of the thermocouple need some respond time during the process of sensor, if water flowing is too large, it is easy to cause rigid material, the foam sheet extruded will be bubble, it will be broken hole seriously, even cracking strip one strand by one strand, so, should checking the temperature of each zone during the cooling, adjusting the water flow corresponding.
b. Screen exchanger and machine head.
Turning off the heating knob of machine head and screen exchanger, , to make it stop heating, dipping in water by pieces of cloth, or pouring with small water lowing by water pipeline, to cool for screen exchanger and machine head, it should be intermittent of cooling by pouring to avoid cooling fast to cause the rigid material at the screen exchanger and machine head position. Notice: before pouring on machine head and the screen exchanger, be sure that the heating power is cut off to prevent electric shock.
Operating during cooling process.
Adjusting the die clearance.
Turn machine head to adjust the nut, make the inside and outside die gap is 0.1-0.2mm. Turning down the die gap appropriate can reduce the waste. Checking the extruded material thickness die around, adjusting the inside die position to make it uniform through the jackscrew. If there is cracking phenomenon on ethe sheet extruded, showing there is dirty things at the gap of die, should to loose the adjusting nut , and tighten it back, to let the dirty thins go outside.
Notice: The gap of EPE foaming machine(Expanded polyethylene machine) mould should be adjusted suitable, smaller then will easily to make sheet crack, and bigger will make it with deflated voice.
The controlling of machine engine HZ, temperature, butane and monostearin.
When the temperature of any zone in 6th , 7th , 8th cooling zone down to the set temperature, should adjust the machine engine frequency to normal production request frequency according to the sheet thickness, then increase the flow of butane and monostearin to suitable value (each value should refer to the value when testing running machine) Here must notice that, if butane flow is larger, the machine head will easy to has airblast ; if flow is less, the foaming will not so good, to cause the barrel pressure is higher.
If the monostearin flow is much larger, it is also easy to has airblast in machine head; less, the material will easy to stick on the surface of mould, then the sheet extruded will be easy to shrink. The way to check if there is monostearin is: to make the foam sheet soak in water for a while, checking if there is white foam bubble, if it is, showing there is monostearin.
Observing the material extruded from machine head, judging the cooling level, when the edge is not stick with each other between the foam sheet, adjusting the die gap according to the sheet thickness, and adjusting the jackscrew through the inside die to let the extruded sheet thickness is uniform. Cleaning the materials adhere tothe die. If the edge of sheet is adhesion, checking if the temperature of screen exchanger and machine head has downed to set temperature, if the temperature is higher, cooling continuously, if it has been reached the set one, then it maybe the temperature of outside and inside mould is higher, wiping the mould by wet cloth, untill the edge doesn’t adhere with each other again.
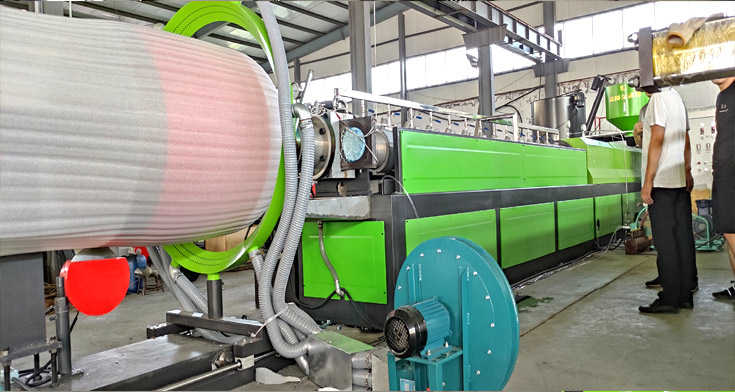
Starting the sizing drum fan , wind ring fan and cutting fan.
Starting the traction and rolling machine, and adjusting the speed of them.
Separate the tubular foaming sheet from machine head, moving the sizing drum to align the machine head, to let the foaming sheet cover over the sizing drum, pulling and tear off the defective material on the top , through the flatten frame to traction machine, finally to the rolling machine, rolling it on the paper tube of roller quickly, adjusting the traction speed and rolling speed, to let it match with the foam sheet extruding speed.
After the sheet covering the sizing cylinder , moving the vane to the front of the sizing cylinder, don’t let the wind from vane blow to the machine head.
Ensure the machine heading temperature is not higher than set temperature, turn on the screen exchanger and machine head heating switch.
Checking the foam sheet thickness, if it is near to the requirement, adjusting the traction speed, to make the sheet reach to the requirement; if it is far away the requirement, then adjusting the die gap firstly, then adjusting the traction speed, untill it is your request thickness.
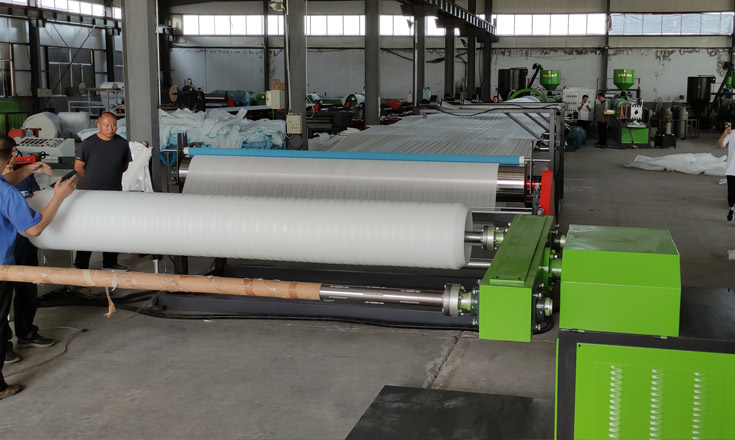
According to the quality request, checking the sheet bubble size, corrugated height, width and the shrinkage , to ensure the flowing of talcum powder, butane, monostearin and temperature is ok.
When it is in the middle of rolling,patting the sheet roll by hand along the axial, it should be uniform feels in everywhere. Otherwise, if feels loose, then it shows the sheet is thin here, if feels tighten, then shows the sheet is thick, so should adjusting the inner die jackscrew a little, to clear away this phenomenon.
If this is the first time to start machine, it should adjusting the flatten frame height and location, and the traction and rolling machine ‘s location, to ensure the rolling working can be smooth and tidy.
when the foam sheet reached the set length, the machine will automatic rollover to change the loca