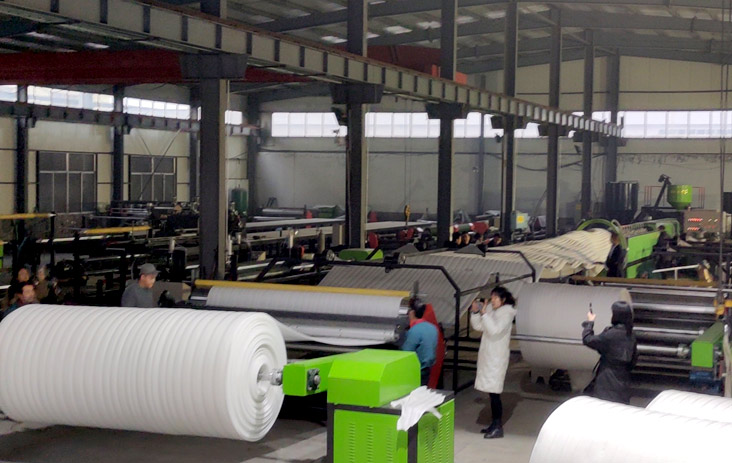
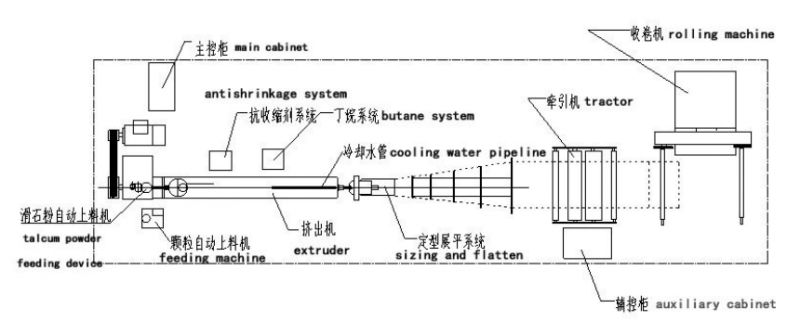
Screw: It is made of 38CrMnALA nitrided steel. After heat treatment and tempering, nitriding treatment and surface treatment chrome plating, the screw has the characteristics of high strength and high surface hardness, thereby increasing the service life of the screw of EPE foam sheet production line. The screw s L/D ratio =55:1 (ratio between length and diameter), which improves the plasticizing capacity and quality of the screw.
Barrel: It is made of 38CrMnALA nitrided steel. After heat treatment (tempering + nitriding), it can prevent loss caused by long-term use. The barrel, the feed section and the die device are connected by flanges.
Feeding section: Both ends of the feeding section of the EPE foam sheet production line are connected to the barrel and the gearbox respectively. Raw material is fed into the extruder from this part. The user should maintain the continuous circulation of the cooling water of this part to prevent the temperature from rising which might cause the raw materials to become sticky, agglomerate, and block the feed inlet.
The main motor of the extruder: the main motor is an AC motor with inverter, which is cooled by air (equipped with a cooling fan). The main motor is connected to the screw through a reduction box.
Butane input and butane pump: The butane pump is a high-pressure metering pump. This pump injects liquefied butane into the barrel at a high pressure of 10--40Mpa. Butane and melted LDPE are mixed at the entry into the barrel. There is a one-way valve where the butane enters the barrel to ensure that the melted LDPE will not flow backward when the barrel pressure is greater than the butane pressure, ensuring production safety.
Anti-shrinking agent input and anti-shrinking agent pump: The anti-shrinking agent pump sends the anti-shrinking agent into the screw and barrel of the EPE foam sheet production line after heating it at a pressure of 10-40Mpa. The melted anti-shrinking agent and LDPE are mixed in the feeding part where anti-shrinking agent enters the screw. This feeding part is equipped with a one-way valve to prevent the melted LDPE from flowing backward when the barrel pressure is higher than the pressure of the anti-shrinking agent to ensure production safety.
Die head part: The melted raw material is extruded from this part. The raw material begins to foam as soon as it passes through the lip of the mold. The thickness of the EPE sheet depends on the mould lip size of the EPE foam sheet extruding line and the traction speed.
Shaping barrel: The width of the EPE sheet is determined by this part, so cooling water and cooling air should be provided in this part.
Traction roller: The sheet stretched by the shaping barrel enters this part for traction. At this time, the traction speed should be equivalent to the production speed to ensure the quality of the sheet. The traction roller has a diameter of φ350~2200mm, and is equipped with motor with inverter to adjust the traction speed.
Winding machine with double-station and automatic meter counting and overturning: This part is equipped with a meter counter that can set the length of the sheet. When the length of the first roll reaches the set requirement, it can be automatically turned over 180° and the second axis starts automatically turn over and wind and the first axis will stop automatically.